|
На производстве метанола работы проводились в цехе КПД,
отделениях МЭО и дегазации в основном на насосном оборудовании - обработка
подшипниковых узлов, и цехе компрессии метанола - полная обработка азотного
компрессора 4НР/5, на компрессорах ТЦК - обработка подшипниковых узлов.
Всего
прошли обработку ТС "НИОД" 76 единиц оборудования.
На производстве капролактама работы проводились в цехе
лактама, отделении кристаллизации и цехе циклогексана. В цехе циклогексана
обработаны 2-а водородных компрессора 5Г-600/42-60 (полная обработка), ряд
вентиляторов ВЛ - 20А, теплогенератор. В отделении кристолизации - редукторы,
вентиляторы, в цехе лактама — подшипниковые узлы насосного оборудования. Всего
по производству капролактама произведена обработка ТС "НИОД" 181 единица
оборудования. В целом по ОАО "Щекиноазот" обработано 257 единиц оборудования, с
учетом повторных обработок 361 единица.
Насосное оборудование цеха
КПД.
В
целях определения эффективности применения триботехнического состава на насосном
оборудовании производства отслежены три группы наиболее крупных и наиболее
загруженных насосов в цехе КПД. Выборка аварийных выходов производилась по
ремонтным журналам с 1.01.1997г. по 20.12.1999г.
Срок безаварийной работ подшипников
увеличился по группе насосов НМА в 5 раз, по группе насосов НД в 1,6 раза.
До настоящего времени продолжают работать без выходов по группе НМА – 3 единицы. Экономия подшипников №№ 66322, 320, 3618, 216 за счет увеличения сроков
безаварийной работы, после обработки ТС "НИОД" составила - 51шт.
Компрессоры ТЦК.
Анализ выходов подшипников ТЦК в 1996—1997г.г.
показывает, что в 2/3 случаев аварийных остановок ТЦК причиной является выход
подшипников электродвигателей, и только 1/3 случаев - выход подшипников
компрессора. Учитывая, что причиной выхода из строя подшипников компрессора
является не только трение, но и прорыв метанола, выносы катализатора и другие
причины было принято решение обрабатывать только подшипники электродвигателей и
за счет увеличения сроков их ходимости добиться общего увеличения безаварийной
эксплуатации ТЦК. С этой целью, на всех выходивших в ремонт ТЦК, при установке
на двигатель новых подшипников, проводилась их обработка ТС "НИОД".
Количество выходов подшипников компрессора уменьшилось с 10-и
в 1997г. до 6 случаев в 1999 г., что говорит о значительном повышении надежности
работы подшипниковых узлов электродвигателя. Средний срок безаварийной
эксплуатации одного ТЦК, после обработки ТС "НИОД" подшипников электродвигателей,
увеличился с 62 дней до 104 дней. Увеличение сроков ходимости подшипников ТЦК в
1,7 раза против их работы на штатной смазке позволило уменьшить количество
аварийных остановок.
Азотный компрессор 4 НF/5 № 1.
В результате проведённых испытаний компрессор был
выведен на режим эксплуатации с подачей масла через лубрикаторы в количестве 213
капель в минуту (74 капли — 4-5 ступень, 149 капель — 1-3 ступень ), против 791
капли (283 капли — 4-5 ступень, 508 капель — 1-3 ступени ) до обработки.
Поставленная цель была достигнута. Общее снижение
подачи масла через лубрикаторы снижено в 3,7 раза против фактического, в том
числе на 4-5 ступени 3,8 раза против факта и в 2 раза против проекта. В этом
режиме компрессор эксплуатировался до 1999г. Осуществлялся контроль за режимом
подачи масла через лубликаторы и отслеживался температурный режим узлов трения.
На протяжении 1998г. компрессор показывал стабильную надежную работу.
Температура узлов трения в сравнении с контрольным компрессором была ниже на 3-10 °С .
За время работы 4 HF/5 № 1 до обработки и после при
различных режимах по прибору потребляемой мощности отслеживались показатели.
Потребляемая мощность после обработки компрессора снизилась на 100 - 150 квт/час,
в зависимости от режима эксплуатации компрессора.
Производство капролактама.
Цех циклогексана.
Учитывая незначительные сроки эксплуатации от 2 месяцев
до полугода обработанного оборудования (два водородных компрессора 5т—600/42—60
№4 и №3, два вентилятора ВМ-20 А и теплогенератор ТГ - 450 - 1.08). Определить
результаты от внедрения ТС "НИОД" на этом этапе можно только по вторичным
признакам. Одним из таких признаков — температурный режим эксплуатации
оборудования до и после обработки. После обработки температура корпусов в
районах подшипниковых узлов ВМ—20 А снизились на 10-15°С на ТГ—450—1.08 на
6-8°С. В летний период режим оставался прежним (порядка 50-60°С). При
эксплуатации на штатной смазке температура при летней эксплуатации возрастает на
10-20°С, против зимней.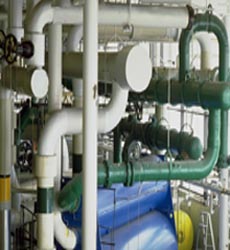
Другим признаком, по которому можно определить наличие результата (подтверждение
снижения трения в узлах) - это потребление электроэнергии механизмом до и после
его обработки.
Технология ТС "НИОД" в своей основе является
энергосберегающей технологией, увеличение сроков эксплуатации в первую очередь
определяется резким снижением коэффициента трения в узлах, следовательно и
потребление электроэнергии должно быть меньше, т. к. на преодоление трения после
обработки требуется значительно меньшая (на порядок) работа.
Такой эксперимент был проведен на компрессоре 5
Г—600/42-60 №4 кор.355. Специально для этих целей энергослужбой производства для
этого компрессора был установлен электросчетчик. Показания счетчика
отслеживались при различных режимах нагрузок компрессора с 25.02.99г. по
13.04.99г. Всего произведено 12 замеров. Нагрузка определялась по разнице
давлений всоса и нагнетания (в МГа). Исключив показания при одинаковых нагрузках
за это время удалось зафиксировать 6 различных показаний счетчика при нагрузках
компрессора — 2,6; 4.3; 4,7; 5,1; 5,6 и 6,0 МПа. Показания счетчика
фиксировались по времени (секундомером ) за 10 оборотов диска счетчика.
Аналогичные показания отслеживались с 9.08. 1999г. по 29. 11. 1999г.
Результат: Снижение потребляемой электроэнергии при
нагрузках в 3 Мпа — 6,2% при нагрузках 3-5 Мпа — 13-14 % . Снижение потребления
в час при нагрузках в 3 Мпа — 11 квт; 4 Мпа — 28 квт; 5-6 Мпа — 40-45 квт.
Цех лактама.
Работы по использованию ТС "НИОД" в подшипниковых узлах
насосов цеха лактама проводятся с июля 1997г. С этого времени все насосы ,
выводящиеся в ремонт по причине выхода из строя подшипников, при ремонте
проходят обработку путем донесения ТС "НИОД" до поверхностей трения через
консистентную смазку. Часть подшипниковых узлов обрабатывается ТС "НИОД" без
остановки механизмов с подачей в узлы трения через жидкую смазку. При наличии в
подшипниковых узлах насосов тавотниц ТС "НИОД" доносится до пар трения с
добавляемой во время эксплуатации штатной смазкой. В сроки с июля 1997г. по
январь 1998г. в цехе лактама обработаны ТС "НИОД" тем или иным способом, все
позиции насосов. В указанный период имелись 103 случая выхода подшипников из
строя.
Отслеживание аварийных выходов подшипников в 1998—1999
г.г. по этой группе механизмов в сравнении с 1997г. позволяет оценить
эффективность ТС "НИОД" - увеличение сроков эксплуатации подшипников, после их
обработки возросли в 4,3 раза. Увеличение ходимости подшипников позволило за
отслеживаемый период уменьшить количество аварийных остановок насосов по причине
выхода из строя подшипников на 325 случаев и соответственно сократить расход
подшипников на 650 шт.
Выводы:
Рассмотренные результаты показывают высокую
эффективность применения ТС "НИОД" в трущихся парах различных видов
оборудования. Разнообразие рассмотренных примерок гарантирует аналогичные
результаты и по другим видам оборудования прошедшим обработку, по которым не
произведен сравнительным анализ в настоящем отчете.
Оценка экономического эффекта за счет
снижения энергозатрат:
|
Снижение
потребления электроэнергии механизмами после обработки их ТС "НИОД" составляет
3-15% (от начального потребления -
до обработки) в зависимости от
режима работы и вида оборудования. Учитывая незначительное количество видов
оборудования, по которым конкретно определялся уровень снижения электроэнергии
остановимся для объективности оценки на нижнем уровне - 3 %.
Fэ = 0,5 * 0,6 *
Wоб * Тт * 0,35 * 0.03 где:
0,5
— коэффициент использования оборудования;
0,6
— коэффициент потребляемой мощности;
W
— сумма мощностей электродвигателей, обработанного оборудования;
0,35
— стоимость одного квт.часа;
Тт — срок работы механизмов после обработки
ТС "НИОД" - 24 месяца (17 568 час.);
Fэ = 0,6 * 0,6 * 30480
* 17568 - 0,35 * 0,03
= 2024065
рублей.
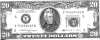 |
Оценка эффективности
применения ТС "НИОД":
|
Общий объём снижения затрат, полученных от внедрения ТС "НИОД":
Fоб. =
1 969 000 + 113 680 + 2 024 065 =
4 106 745
рублей;
Qз —
сумма затрат по внедрению ТС "НИОД" за весь период работы
составила 468 300 рублей;
Э
— экономический эффект;
Э = Fоб. - Оз =3 638 445
рублей;
Окупаемость затрат: Э/Qз
= в 8 раз
.
В том числе Эт — экономический эффект от увеличения сроков
безаварийной работы подшипниковых узлов оборудования.
Эт = 1 969 000 – 468 300 = 1 500 700
рублей.
|
|